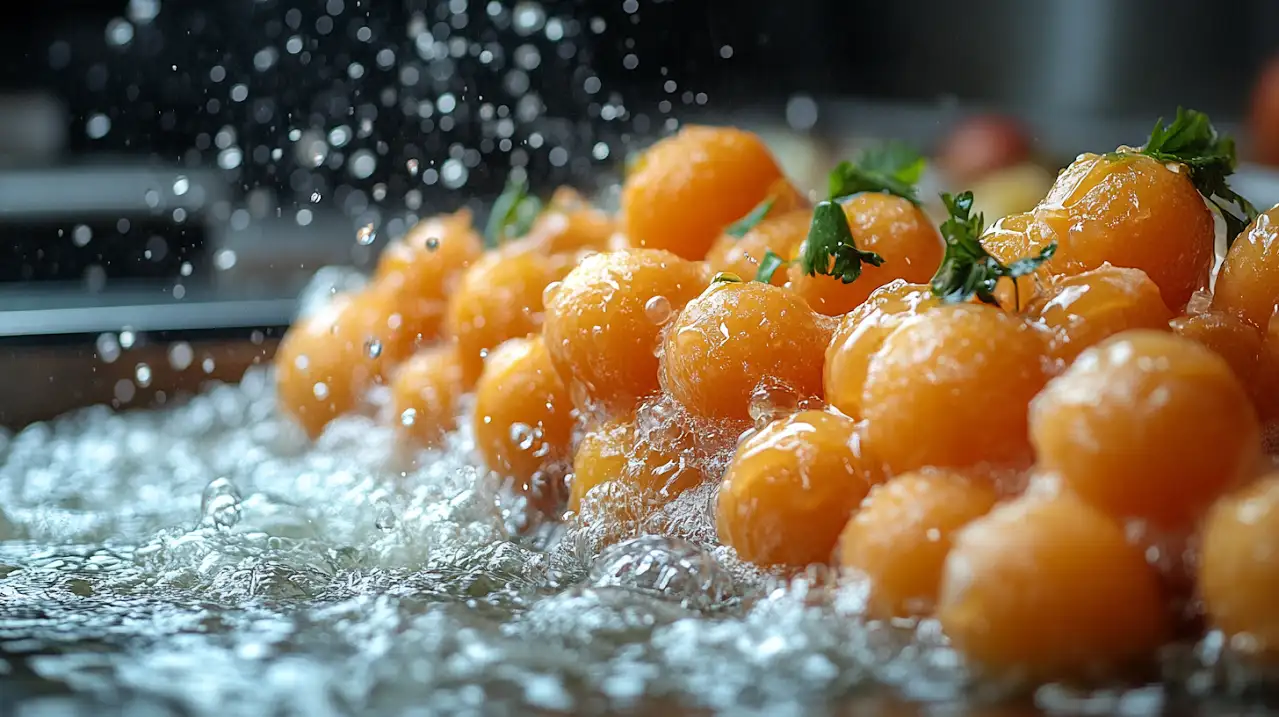
Automation Revolution in Food Storage Operations
The UAE’s commitment to food security has catalyzed a remarkable transformation in warehouse automation, with investments exceeding AED 5.6 billion in smart storage solutions since 2022. Modern facilities now utilize advanced robotics systems capable of handling 15,000 pallets daily with 99.99% accuracy. These automated storage and retrieval systems (AS/RS) operate in high-bay warehouses reaching heights of 42 meters, maximizing storage density while reducing the facility footprint by 60% compared to traditional warehouses.
The integration of artificial intelligence has revolutionized inventory management, with machine learning algorithms predicting demand patterns with 94% accuracy up to 30 days in advance. These systems process data from over 50,000 SKUs simultaneously, optimizing stock levels and reducing excess inventory by 37%. Smart shelving systems equipped with weight sensors and RFID technology provide real-time inventory updates, eliminating manual counting and reducing stock discrepancies by 89%.
Automated guided vehicles (AGVs) have transformed internal logistics, with fleets of up to 100 robots per facility operating 24/7 to move products between storage zones. These vehicles navigate using LIDAR technology and advanced mapping systems, achieving positioning accuracy within 5mm while reducing labor costs by 65% and improving workplace safety by eliminating 95% of manual material handling tasks.
The implementation of conveyor systems with integrated sorting capabilities has increased throughput to 20,000 cases per hour, while reducing product damage by 78%. These systems utilize computer vision technology to inspect packages for damage and verify proper labeling, ensuring quality control throughout the movement process. The automation infrastructure has reduced order processing times by 82% while improving accuracy to 99.98%.
Intelligent Environmental Control Systems
Smart warehousing facilities in the UAE employ sophisticated environmental control systems that maintain optimal storage conditions through a network of over 2,000 IoT sensors per facility. These systems monitor temperature, humidity, air quality, and atmospheric composition in real-time, making automatic adjustments to maintain ideal conditions for different food products. The implementation of zone-specific environmental controls has reduced energy consumption by 45% while extending product shelf life by up to 40%.
Advanced HVAC systems utilize predictive analytics to anticipate temperature fluctuations based on factors such as door openings, product movement, and external weather conditions. These systems adjust cooling capacity proactively, maintaining temperature stability within ±0.2°C while reducing energy consumption by 38%. The integration of smart ventilation systems ensures 12-15 air changes per hour in storage areas, maintaining optimal air quality while minimizing energy waste.
Humidity control systems employ advanced desiccant technology capable of maintaining relative humidity levels within ±2% of target values. These systems process up to 50,000 cubic meters of air per hour, removing excess moisture while preventing product dehydration. The implementation of these systems has reduced product loss due to moisture-related issues by 92% while improving energy efficiency by 35%.
The facilities utilize advanced air filtration systems that remove 99.97% of airborne particles down to 0.3 microns, maintaining clean room conditions in sensitive storage areas. These systems integrate UV-C sterilization technology that eliminates up to 99.99% of airborne pathogens, reducing the risk of product contamination while ensuring worker safety.
Inventory Analytics and Demand Forecasting
The implementation of advanced analytics platforms has transformed inventory management in UAE’s smart warehouses. These systems process over 100 million data points daily, utilizing artificial intelligence to optimize stock levels and reduce waste. Machine learning algorithms analyze historical data, seasonal patterns, and market trends to predict demand with 95% accuracy, reducing overstock situations by 67% while maintaining 99.9% product availability.
Real-time inventory tracking systems utilize a combination of RFID, computer vision, and weight sensors to maintain accurate stock counts without manual intervention. These systems track product movement with millisecond accuracy, enabling automated reordering when stock levels reach predetermined thresholds. The integration of blockchain technology ensures transparency and traceability throughout the supply chain, reducing audit times by 85% while improving stakeholder confidence.
Advanced analytics tools process data from multiple sources, including point-of-sale systems, weather forecasts, and social media trends, to optimize inventory levels dynamically. These systems have reduced working capital requirements by 42% while improving inventory turnover rates by 58%. The implementation of predictive maintenance algorithms has reduced equipment downtime by 75%, ensuring consistent operation of critical storage systems.
Digital twin technology creates virtual replicas of warehouse operations, enabling managers to simulate different scenarios and optimize processes without disrupting actual operations. These simulations have improved space utilization by 34% while reducing operating costs by 28%. The system processes real-time data from thousands of sensors to maintain accurate virtual representations, enabling proactive decision-making and continuous improvement.
Last-Mile Distribution Optimization
Smart warehousing facilities in the UAE have revolutionized last-mile distribution through the integration of advanced routing and delivery management systems. These platforms process real-time traffic data, weather conditions, and delivery time windows to optimize delivery routes, reducing transportation costs by 35% while improving on-time delivery performance to 99.8%. The implementation of dynamic routing algorithms has reduced average delivery times by 42% while decreasing fuel consumption by 28%.
Loading dock management systems utilize predictive analytics to schedule vehicle arrivals, reducing wait times by 85% and optimizing dock utilization. These systems coordinate with automated picking systems to ensure orders are ready for loading precisely when vehicles arrive, reducing loading times by 67%. The integration of mobile applications provides real-time visibility to drivers and customers, improving communication and reducing failed deliveries by 92%.
Cross-docking facilities equipped with automated sorting systems process up to 100,000 packages daily, reducing handling time by 78% while improving accuracy to 99.99%. These systems utilize computer vision and AI to sort packages based on destination, optimizing load building and route efficiency. The implementation of these systems has reduced cross-docking times from hours to minutes, enabling same-day delivery for urgent orders.
Smart loading systems utilize 3D scanning technology to optimize vehicle load patterns, improving capacity utilization by 45% while ensuring proper weight distribution. These systems consider product characteristics, delivery sequence, and vehicle specifications to generate optimal loading plans, reducing product damage during transport by 88%.
Workforce Enhancement Through Technology
The integration of advanced training systems and augmented reality technology has transformed workforce management in smart warehouses. Digital training platforms utilize virtual reality simulations to provide hands-on experience with complex equipment and procedures, reducing training time by 65% while improving skill retention by 85%. These systems enable workers to practice emergency procedures and unusual scenarios without risk, improving safety awareness and response capabilities.
Wearable technology, including smart glasses and exoskeletons, has enhanced worker productivity while reducing physical strain. Smart glasses provide real-time information and picking instructions, improving accuracy by 94% while reducing the time required to locate products by 72%. Powered exoskeletons reduce physical strain during manual handling tasks, decreasing workplace injuries by 85% while improving worker endurance.
AI-powered workforce management systems optimize staff scheduling based on predicted workload, reducing labor costs by 32% while improving productivity by 45%. These systems consider factors such as worker skills, certification requirements, and fatigue levels to ensure optimal staffing levels across all shifts. The implementation of biometric authentication and automated time tracking has improved attendance accuracy while reducing time theft by 98%.
Mobile devices equipped with custom applications provide workers with real-time task assignments, performance feedback, and safety alerts. These systems have improved communication efficiency by 75% while enabling real-time performance monitoring and coaching. The integration of gamification elements has increased worker engagement by 68% while improving overall operational efficiency.
Quality Assurance and Compliance Monitoring
Smart warehousing facilities implement comprehensive quality assurance systems that utilize artificial intelligence and sensor networks to monitor product quality continuously. Advanced imaging systems perform automated quality checks on incoming and outgoing products, detecting defects with 99.9% accuracy while processing up to 1,000 items per minute. These systems maintain digital records of all inspections, reducing documentation time by 90% while improving traceability.
Automated sampling systems utilize robotic arms and conveyor systems to collect product samples according to predefined protocols, ensuring consistent testing procedures while reducing human error. These systems integrate with laboratory information management systems (LIMS) to track sample analysis and maintain compliance records. The implementation of these systems has reduced quality control costs by 45% while improving sampling accuracy by 92%.
Real-time compliance monitoring systems track over 1,000 parameters simultaneously, ensuring adherence to regulatory requirements and industry standards. These systems generate automated alerts when parameters deviate from acceptable ranges, enabling immediate corrective action. The integration of blockchain technology ensures the integrity of compliance records, reducing audit preparation time by 85% while improving stakeholder confidence.
Temperature monitoring systems utilize infrared cameras and wireless sensors to maintain continuous surveillance of storage conditions, generating immediate alerts if temperatures deviate from acceptable ranges. These systems maintain detailed records of temperature history, enabling comprehensive analysis of storage conditions and rapid response to any deviations. The implementation of these systems has reduced temperature-related product losses by 95% while improving regulatory compliance scores.