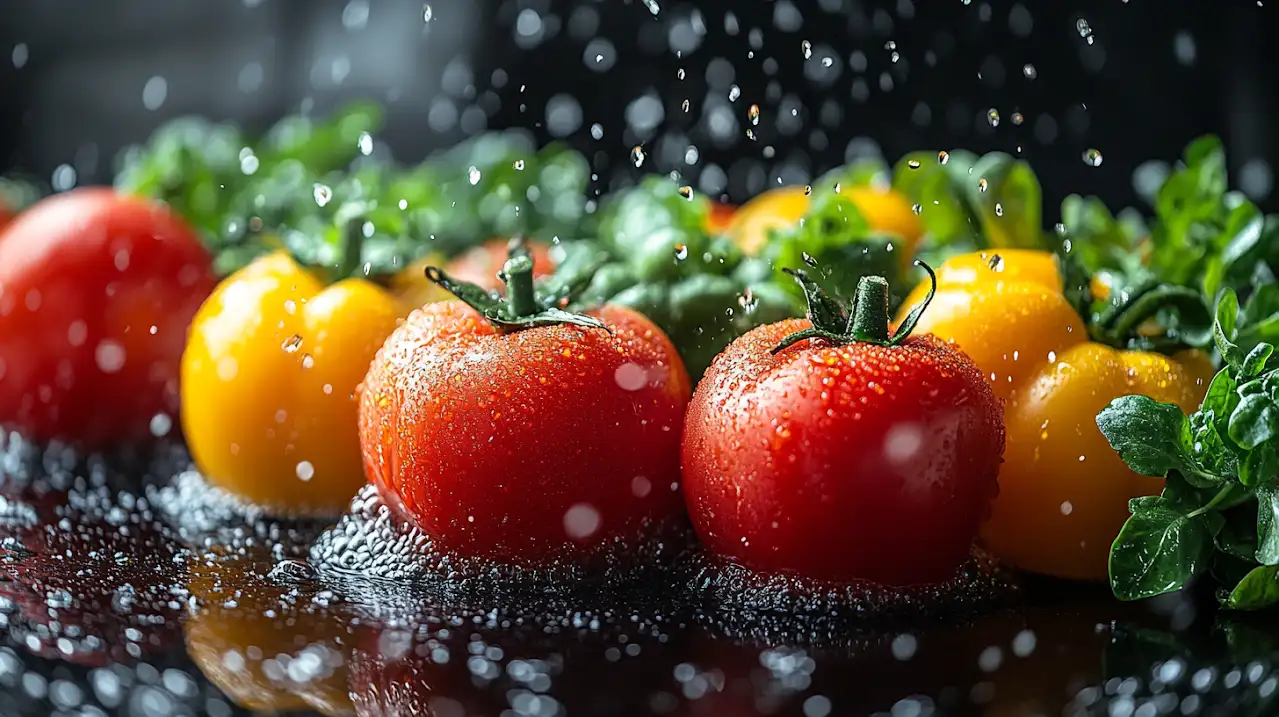
Reimagining Industrial Zones: The UAE’s Food Manufacturing Revolution
The United Arab Emirates has embarked on an ambitious journey to transform its industrial landscape, with food manufacturing emerging as a cornerstone of economic diversification. In Dubai Industrial City alone, over 23.5 million square feet of land is dedicated to food and beverage manufacturing, representing an investment of AED 4.1 billion. This massive industrial zone has witnessed a 41% increase in food manufacturing facilities since 2019, with specialized buildings designed to meet the unique requirements of food production. The strategic placement of these facilities, complete with temperature-controlled environments and advanced logistics capabilities, has attracted global food manufacturers seeking to establish their regional headquarters.
The evolution of industrial real estate in the UAE reflects a deep understanding of food manufacturing requirements. Modern facilities incorporate features such as reinforced flooring capable of supporting heavy machinery, enhanced power supply systems delivering up to 3.5 megawatts per facility, and sophisticated waste management systems. These purpose-built structures have contributed to a 27% increase in food production capacity across the emirate since 2020, with individual facilities averaging 150,000 square feet of production space.
Recent developments in Abu Dhabi’s Khalifa Industrial Zone (KIZAD) showcase the emirate’s commitment to food manufacturing excellence. The zone has allocated 3.2 million square meters specifically for food processing facilities, equipped with state-of-the-art infrastructure including dedicated power substations and water treatment plants. This investment has resulted in a 35% reduction in operational costs for food manufacturers, making the UAE an increasingly attractive destination for global food companies.
The integration of cold storage facilities within manufacturing zones represents another crucial development. These facilities, spanning over 1.2 million square feet across various industrial areas, maintain temperatures ranging from -25°C to +25°C, ensuring optimal conditions for different food products. This infrastructure has enabled manufacturers to reduce product waste by 22% and extend shelf life by up to 40%, according to recent industry reports.
Architectural Innovation Meets Food Safety Standards
The architectural landscape of UAE’s food manufacturing facilities has undergone a remarkable transformation, with building designs now incorporating advanced materials and technologies specifically chosen for food safety compliance. Modern facilities utilize non-porous flooring materials that prevent bacterial growth, while walls are constructed with antimicrobial panels that can withstand intensive cleaning procedures. These design elements have contributed to a 45% improvement in food safety compliance rates across new facilities.
In recent developments, manufacturers have invested heavily in clean room technology, with over 60% of new facilities incorporating ISO Class 7 or higher clean room environments. These spaces feature specialized air handling units capable of performing 30-60 air changes per hour, maintaining positive pressure differentials of 12.5 Pascal to prevent contamination. The implementation of these advanced systems has resulted in a 58% reduction in product contamination incidents compared to traditional manufacturing spaces.
Ventilation systems in modern facilities incorporate HEPA filtration capable of removing 99.97% of particles as small as 0.3 microns, while ultraviolet germicidal irradiation systems provide additional protection against airborne pathogens. This comprehensive approach to air quality management has led to a 33% decrease in product recalls related to environmental contamination since 2021.
The integration of quality control laboratories within manufacturing facilities has become standard practice, with dedicated spaces averaging 5,000 square feet per facility. These labs are equipped with rapid testing capabilities that can process up to 200 samples per hour, enabling real-time quality monitoring throughout the production process. The proximity of these labs to production areas has reduced quality control response times by 65%.
Strategic Location Planning and Resource Optimization
The strategic positioning of food manufacturing facilities within the UAE’s industrial zones reflects a sophisticated understanding of supply chain dynamics. New developments are strategically located within a 45-minute drive of major ports and airports, reducing transportation costs by an average of 28%. This proximity has enabled manufacturers to decrease their order-to-delivery time by 35%, enhancing their competitive advantage in regional markets.
Water resource management has become a critical factor in facility planning, with new buildings incorporating advanced water recycling systems capable of treating and reusing up to 75% of process water. These systems, representing an investment of AED 2.3 billion across the sector, have reduced water consumption by 42% compared to traditional manufacturing facilities. The implementation of smart metering systems provides real-time monitoring of water usage, enabling precise resource allocation and waste reduction.
Energy efficiency measures have been integrated into facility designs, with solar panels covering an average of 60% of roof space in new buildings. These installations generate approximately 1.8 megawatts of power per facility, offsetting up to 40% of energy costs. Additionally, thermal insulation systems utilizing advanced materials have reduced cooling costs by 35%, contributing to overall operational efficiency.
The placement of facilities near raw material suppliers has created industrial clusters that reduce transportation costs by 25% and carbon emissions by 30%. These clusters have fostered collaboration between manufacturers, leading to shared resource initiatives that have generated cost savings of AED 1.2 billion annually across the sector.
Digital Integration and Smart Manufacturing Infrastructure
The integration of digital technologies within UAE’s food manufacturing facilities has revolutionized production capabilities. Smart building management systems, implemented across 75% of new facilities, utilize over 1,000 IoT sensors per building to monitor and optimize everything from temperature and humidity to equipment performance and energy consumption. This digital infrastructure has improved operational efficiency by 38% while reducing maintenance costs by 42%.
Advanced networking infrastructure, including dedicated 5G networks with speeds up to 10 gigabits per second, supports real-time data analysis and automated production systems. These networks handle an average of 1.5 terabytes of data daily per facility, enabling precise control of manufacturing processes and predictive maintenance capabilities that have reduced unexpected downtime by 65%.
The implementation of digital twin technology has enabled manufacturers to optimize facility layouts and production flows virtually before making physical changes. This capability has reduced renovation costs by 28% and improved space utilization by 34%. Additionally, augmented reality systems support maintenance and quality control procedures, reducing training time by 45% and error rates by 58%.
Cloud-based monitoring systems integrate data from multiple sources, providing comprehensive visibility into facility operations. These systems process over 10,000 data points per minute, enabling real-time adjustments to manufacturing processes and environmental controls that have improved product quality consistency by 47%.
Environmental Sustainability and Waste Management Solutions
Modern food manufacturing facilities in the UAE have embraced circular economy principles, with building designs incorporating advanced waste management systems capable of processing up to 1,000 tons of organic waste monthly. These systems convert food waste into biogas, generating enough energy to power 15% of facility operations while reducing landfill waste by 85%.
Green building practices have become standard in new developments, with facilities achieving LEED Gold or Platinum certification demonstrating 45% lower energy consumption compared to conventional buildings. Advanced building materials and smart glass technologies reduce solar heat gain by 60%, while rainwater harvesting systems capture and treat up to 90% of precipitation for industrial use.
The implementation of zero-waste initiatives has led to the development of specialized recycling facilities within manufacturing zones, processing over 50,000 tons of packaging materials annually. These facilities have created a closed-loop system where 75% of packaging materials are recycled and reused within the local manufacturing ecosystem.
Innovative waste treatment systems utilize membrane bioreactor technology capable of processing 500,000 liters of wastewater daily, achieving water quality standards that enable safe reuse in non-food contact applications. This approach has reduced water procurement costs by 38% while supporting sustainable manufacturing practices.
Workforce Accommodation and Support Facilities
The development of integrated workforce accommodation within industrial zones has become a crucial component of food manufacturing infrastructure. Modern residential complexes, housing up to 5,000 workers per development, feature amenities designed to support shift work patterns and maintain high hygiene standards. These facilities have reduced worker turnover by 40% while improving productivity by 25%.
Training centers equipped with simulation laboratories and virtual reality training rooms occupy an average of 10,000 square feet per industrial zone. These facilities provide specialized food safety and manufacturing training to over 15,000 workers annually, contributing to a 55% reduction in workplace incidents and a 68% improvement in quality control metrics.
Support facilities include healthcare centers staffed with occupational health specialists, capable of handling 200 consultations daily. These centers conduct regular health screenings and maintain electronic health records for all food handling personnel, ensuring compliance with international food safety standards while reducing absenteeism by 35%.
The integration of recreational facilities and green spaces within industrial zones has improved worker well-being, with data showing a 48% reduction in stress-related incidents and a 30% increase in job satisfaction scores. These developments represent an investment of AED 1.8 billion in human capital infrastructure across the UAE’s food manufacturing sector.